Welding Without a Flame? Friction Welding Explained!
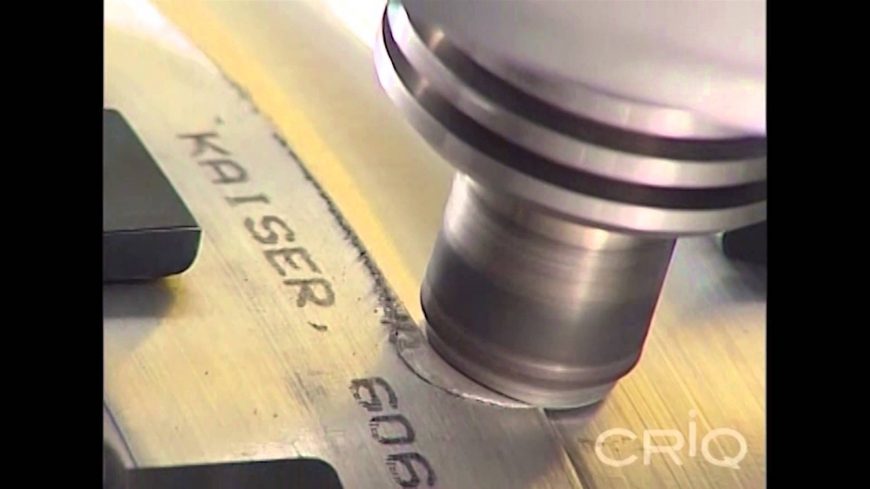
When it comes to processes like commercial welding and many other intermediate steps that go into creating a final product, businesses are obviously looking for any way that they can to save money. When you crank out a large amount of a product, every penny saved could go a long way toward the bottom line by taking off thousands of dollars from your costs if not more! With that in mind, friction welding could have it all!
This time, we check out a process that could save money and potentially provide more benefits than other traditional forms of welding as we watch inertia friction welding unfolding in front of our eyes in order to bond together turbine engine components. The process might not be how you’re used to seeing a weld get done but it does look to be pretty effective nonetheless.
In this one, we watch as metals are rubbed together with an incredible rate of force and speed, creating friction as the name implies which heats the metals up and melts them together to fuse them to one another. When the melted metal cools, you’re left with a solid weld that is said to have the potential to be even stronger and more thorough than a traditional surface weld.
A quick search told us that this kind of welding can be beneficial when you’re looking to combine two different kinds of metals that couldn’t be traditionally welded together or are looking to weld together materials without having to prepare and clean them so much. It most certainly seems to be not only a process that could provide a better weld but also one that requires less talent and could be much easier to automate. Check out the video below that takes us on the scene that shows exactly how friction welding happens.
https://www.youtube.com/watch?v=aNbQH8XBgxQ