Turbochargers Need to be Made Perfectly – This is How They do It
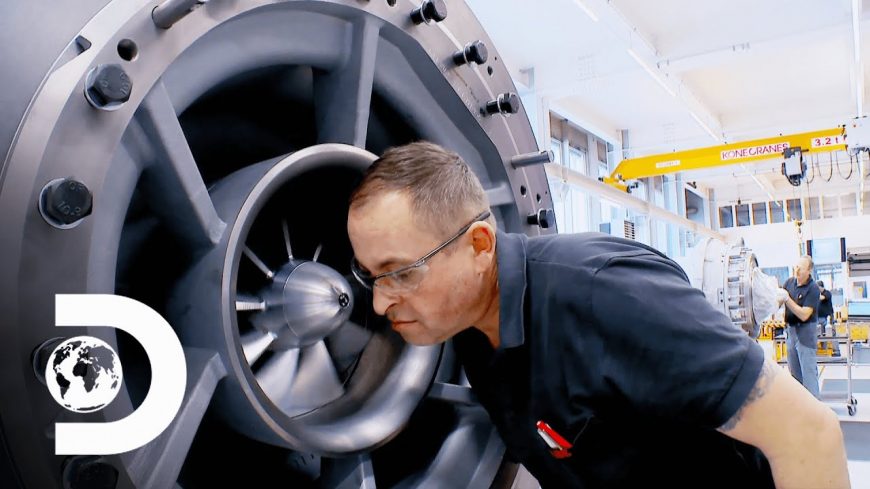
Within any given automobile, there are a ton of parts working together in unison to create the finished product. Every button that we push or knob that we twist has an outcome that we don’t think much about. However, these outcomes are on the heels of lots of different processes occurring simultaneously in order to make the different functions come to life.
This idea is very real when it comes to pushing down the throttle. As soon as somebody lays into the accelerator, a bunch of processes simultaneously uncork themselves so that the vehicle can propel itself forward. It just so happens that, when some sort of forced induction is involved, there are a couple of more steps to be considered. The fun part is that these steps often yield more power.
This time, we take it one step further. Not only are we talking about the pieces coming together to make the car move. We also like to consider what exactly it is that makes each component within those processes absolutely perfect. When all is said and done, these pieces of metal and plastic need to be accurate to size within thousands of an inch. Anything else would guarantee that they won’t work properly at a minimum and completely destroy essential components on their bad days. That’s definitely not something that anybody wants to be a part of.
By following along with the video below, we get taken inside of the precise process that brings together turbochargers. After checking this one out, we think that most people will get an all-new appreciation for that spooling and sputtering forced induction unit underneath the hood. While we’re sure that manufacturers are always improving these processes to make these units come together, where they currently sit today is nothing short of amazing.